The role of carbon black in conveyor belt production
Carbon black is a black powder produced from the incomplete combustion or pyrolysis of hydrocarbons under strictly controlled process conditions. Its main component is elemental carbon, with small amounts of oxygen, hydrogen, and sulfur. Carbon black particles are nearly spherical, with diameters ranging from 10 to 500 μm. Many particles often fuse or aggregate into three-dimensional dendritic or fibrous aggregates. In rubber processing, it is added to rubber through compounding as a reinforcing agent (see reinforced materials) and filler. Carbon black is one of the oldest industrial products.
physicochemical property
superficial area
One of the key properties used for identifying and classifying carbon black. The specific surface area is measured using gas-phase or liquid-phase adsorption methods. The most classic method is the low-temperature nitrogen adsorption method (i.e., BET method). Due to the relatively small size of nitrogen molecules, they can enter the micropores of carbon black, and the results obtained from this method characterize the total specific surface area of carbon black. In recent years, successful research has been conducted on macromolecular adsorption methods (such as CTAB), where macromolecules cannot enter the micropores, and the results obtained from these methods characterize the external surface area of carbon black, known as the “smooth” surface area. Most rubber-grade carbon black is non-porous, so the results from BET and CTAB are consistent. For certain pigment-grade carbon black, the difference between these two specific surface area measurements characterizes the roughness or porosity of the carbon black. Another method, ── iodine adsorption, is also widely used in production control and product classification. It is characterized by its simplicity and speed, but the results are influenced by the degree of surface oxidation of the carbon black.
structure
The second important property of carbon black. The structure of carbon black depends on the size, shape, and the number and average mass of particles in each aggregate. These characteristics all influence the packing state of the aggregates and the void volume of the powder. Typically, the structure of carbon black is indicated by its DBP (dibutyl phthalate, dibutyl phthalate) oil absorption value. The DBP value of carbon black after four compressions at 170MPa is conventionally referred to as the compression oil absorption value or 24M4DBP value. The compression oil absorption value more accurately reflects the state of carbon black aggregates in the rubber compound.
Black powder-like substances produced under strictly controlled process conditions through incomplete combustion or pyrolysis of hydrocarbons. Its main component is elemental carbon, with small amounts of oxygen, hydrogen, and sulfur. Carbon black particles are nearly spherical, with diameters ranging from 10 to 500 μm. Many particles often fuse or aggregate into three-dimensional dendritic or fibrous aggregates. In rubber processing, it is added to rubber through compounding as a reinforcing agent (see reinforcing materials) and filler. Carbon black is one of the oldest industrial products. As early as before the Common Era, China used incomplete combustion of plant oils to produce pigment carbon black. In 1872, the United States first produced carbon black using natural gas as a raw material in a tank process. At that time, carbon black was still primarily used as a coloring agent. After S.C. Mott discovered the reinforcing effect of carbon black on rubber in 1912, the carbon black industry rapidly developed. In the 1920s, gas furnace black and thermal cracking black using natural gas as a raw material emerged. R.D. Snow began researching efficient carbon black production methods in 1937. Later, J.C. Creath focused on producing carbon black from liquid hydrocarbons, developing the oil furnace process. The first batch of oil furnace black was produced in 1941. In 1943, the world’s first industrial-scale oil furnace black plant went into operation in the United States. Today, the oil furnace process is the most efficient and economically beneficial method for producing carbon black. Oil furnace black now accounts for 70% to 90% of the total carbon black production.
methods of production
There are three main methods: furnace method, trough method and hot cracking method.
oven process
Black carbon is produced through incomplete combustion or pyrolysis of natural gas or high-aromatic oil in a reactor. This type of black carbon is known as furnace black and is the most abundant and diverse among all types of black carbon. The key difference between furnace black and other forms like trough black and hot cracked black lies in its particle fusion or agglomeration degree, which can be adjusted according to different applications. Therefore, within the same particle size range, furnace black can be divided into several structurally distinct derivatives. Additionally, the oxygen content in furnace black is typically lower than that in trough black (less than 1%), with a neutral or slightly alkaline surface. A characteristic of furnace black production is that the fuel burns in the reactor to provide the heat required for raw material cracking. The combustion and cracking processes occur simultaneously. Depending on the form of the raw materials used, furnace black production can be divided into two methods: gas furnace method and oil furnace method. In the gas furnace method, both the raw materials and fuel are natural gas. For the oil furnace method, the fuel can be natural gas, coke oven gas, or liquid hydrocarbons, while the raw materials include high-aromatic oils such as ethylene tar and anthracene oil. In the furnace black production process (see figure), the reactor is the core equipment. Different reactors with varying structural dimensions are required for producing different types of furnace black. Air and fuel burn in the reactor, and the raw materials are atomized and sprayed into the burning flame, where they undergo high-temperature pyrolysis to form black carbon. The black carbon suspends in the flue gas, which is then rapidly cooled and sent to an air preheater and oil preheater for further cooling before being fed into a bag filter. The separated black carbon is then sent to a granulator for granulation and dried in a dryer.
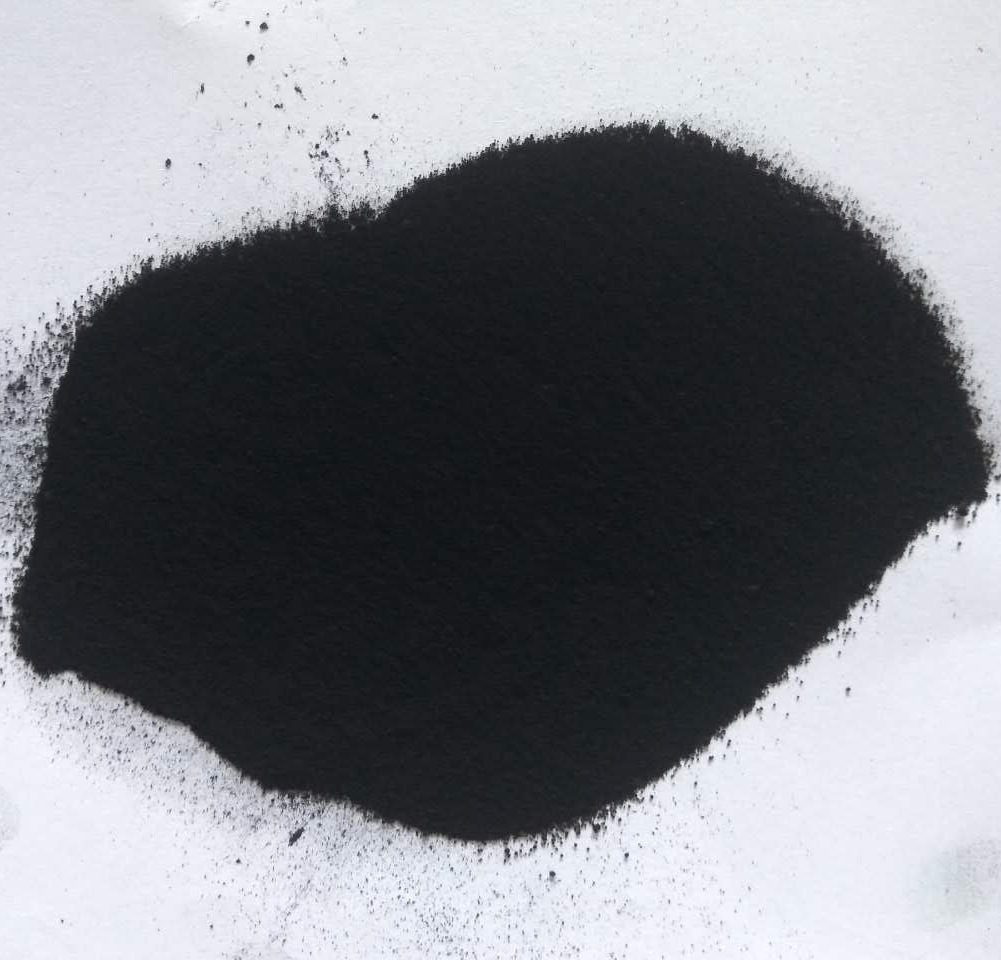
carbon black
channel process
Using natural gas as the main raw material and channel steel as the flame contact surface to produce carbon black, this type of carbon black is called channel black. Compared with furnace black and hot cracked black, its particles are finer and have a larger specific surface area. At the same time, due to the use of specific production methods, its surface is oxidized, containing more oxygen-containing functional groups and thus being acidic. The degree of agglomeration of these carbon black particles is relatively low. Due to the presence of more oxygen-containing functional groups, it can slow down the vulcanization rate of rubber, improve the weather resistance of polyolefins, and give ink good flowability and printing performance.
Thermal cracking method
Using natural gas, coke oven gas, or heavy liquid hydrocarbons as raw materials, carbon black is produced through high-temperature pyrolysis in the absence of oxygen and flame, known as thermal cracked black. It is the type with the lowest specific surface area among carbon blacks, primarily existing as individual spherical particles that do not fuse or aggregate into clusters, with very little oxygen content on its surface (0.1%~0.3%). Thermal cracked black mainly consists of three varieties: medium thermal cracked black, non-polluting medium thermal cracked black, and fine thermal cracked black. The nitrogen adsorption specific surface area of medium thermal cracked black is 6~10 m²/g, while that of fine thermal cracked black is 10~15 m²/g.
Carbon dioxide conversion
The technology developed by the Institute of Thermal Process Engineering at Karlsruhe Institute of Technology (KIT) can extract carbon dioxide directly from the atmosphere and convert it into carbon black.
density
The density of carbon black comes in two forms: true density and apparent density. True density is determined by the elements and structure (or crystal structure) that make up the carbon black. Unless otherwise specified, the density of carbon black refers to true density. Apparent density, on the other hand, varies with processing conditions and requires frequent measurement. Apparent density primarily serves as a basis for calculating the volume of engineering equipment and containers used for packaging and transportation.
The interlayer spacing of carbon black is larger than that of graphite, and its density is lower than that of graphite. The density of carbon black can be measured using various methods, with the most representative being X-ray diffraction and helium displacement. Different testing methods yield different densities for carbon black. The density of carbon black measured by X-ray diffraction is generally 2.O4~2.11Mg·m; the density measured by helium displacement is typically 1.84~2.O6Mg·m, while the density of graphitized carbon black can reach 2.18Mg·m.
In the rubber industry, conventional compounding methods are often used to mix a certain amount of carbon black into rubber of known density, and the density of the carbon black is determined by testing the density of the compound. The carbon black density measured using this method for rubber is generally 1.80~1.86Mg·m³, typically 1.86 Mg·m³. The pouring density of powdered carbon black is usually 30-48 kg·m³, and after densification, it is generally 80-190 kg·m³. The pouring density of wet granulation carbon black is generally 300-500 kg·m³. Carbon black with smaller particle size and higher structure has a lower pouring density.
electrical conductivity
The conductivity of carbon black is closely related to its structure (especially the microcrystalline graphite structure), surface properties, and particle size. The main mechanisms for the conductivity of carbon black in rubber include conductive pathways and field emission. The mechanism of conductive pathways involves the formation of network-like channels through which carbon black aggregates in the compound come into contact with each other, allowing for conduction. The mechanism of field emission occurs when the potential difference between carbon black aggregate chains is sufficiently large, triggering field emission and enabling electrons to jump over the barrier to conduct electricity. Based on these mechanisms, it can be concluded that the smaller the carbon black particles, i.e., the more carbon black particles per unit volume of compound, the greater the probability of contact between particles or the smaller the spacing between particles, resulting in lower resistance and better conductivity. Among carbon blacks with the same particle size, high-structure carbon blacks exhibit better conductivity due to their numerous chain branches, which form more intertwined conductive pathways. Insulating films formed on the surface of carbon blacks with high surface volatility or residual tar-like substances can reduce their conductivity. Heating such carbon blacks in a vacuum or inert gas to remove the surface insulating film enhances their conductivity. The rougher the surface of carbon black, the better its conductivity, as this increases the probability of contact between rougher carbon black particles compared to smoother ones in compounds of the same carbon black content.
In summary, carbon black with small particles, high structure, pure surface, and high surface roughness has good electrical conductivity. When preparing conductive rubber compounds, the amount of carbon black must not be less than a certain critical value; otherwise, insufficient carbon black in the compound will fail to form conductive pathways or trigger field emission, thus failing to meet the required electrical conductivity.
tinctorial strength
Indicators representing the properties of carbon black. A certain amount of carbon black and white pigment (usually zinc oxide or titanium dioxide) is mixed with an oil-based colorant to form a gray ink paste. The scattering ability of this ink paste in visible light is then measured. Carbon black with high coloring strength has a high light absorption coefficient and low reflectivity. The coloring intensity mainly reflects the average volume and size distribution of the aggregates.
Most carbon black has a carbon content of over 97%, while only a few pigments have a carbon content below 90%. In addition to chemically bound oxygen, carbon black also contains water, solvent extracts, sulfur, hydrogen, and inorganic salts on its surface. Hygroscopicity increases with the rise in surface activity, specific surface area, and inorganic salt content. The solvent extracts from carbon black come from hydrocarbons that have not undergone complete thermal decomposition. The sulfur content in carbon black depends on the sulfur content of the raw materials. Inorganic salts mainly originate from quench water and granulation water during the process.
The classification of various types of carbon black often involves their production methods, such as bath black, furnace black, and hot-cracked black. They can also be classified according to their uses, like rubber black and pigment black. The naming principles for carbon black varieties have gradually formed during production and use. Initially, they were represented by abbreviations of English words describing the characteristics and production methods of carbon black, such as HAF for high-wear furnace black and MCC for medium-pigment bath black. The American Society for Testing and Materials (ASTM) established a naming system that primarily defined the naming principles for rubber black. This ASTM naming system has been adopted worldwide. It consists of one letter and three numbers, where the letter indicates the surface properties of the carbon black affecting the rubber processing, with N for normal vulcanization and S for slow vulcanization. The first number after the letter represents the particle size of the carbon black, based on the average particle size measured by electron microscopy, divided into ten grades from 0 for the finest to 9 for the coarsest. The last two numbers are used to distinguish differences in structure and performance. For example, ultra-wear furnace black can be denoted as SAF or N110; high-wear furnace black as HAF or N330; high-wear, high-structure furnace black as HAF-HS or N347; semi-reinforced furnace black as SRF or N770, and easily mixed bath black as EDC or S300.
It plays a role in rubber conveyor belt production
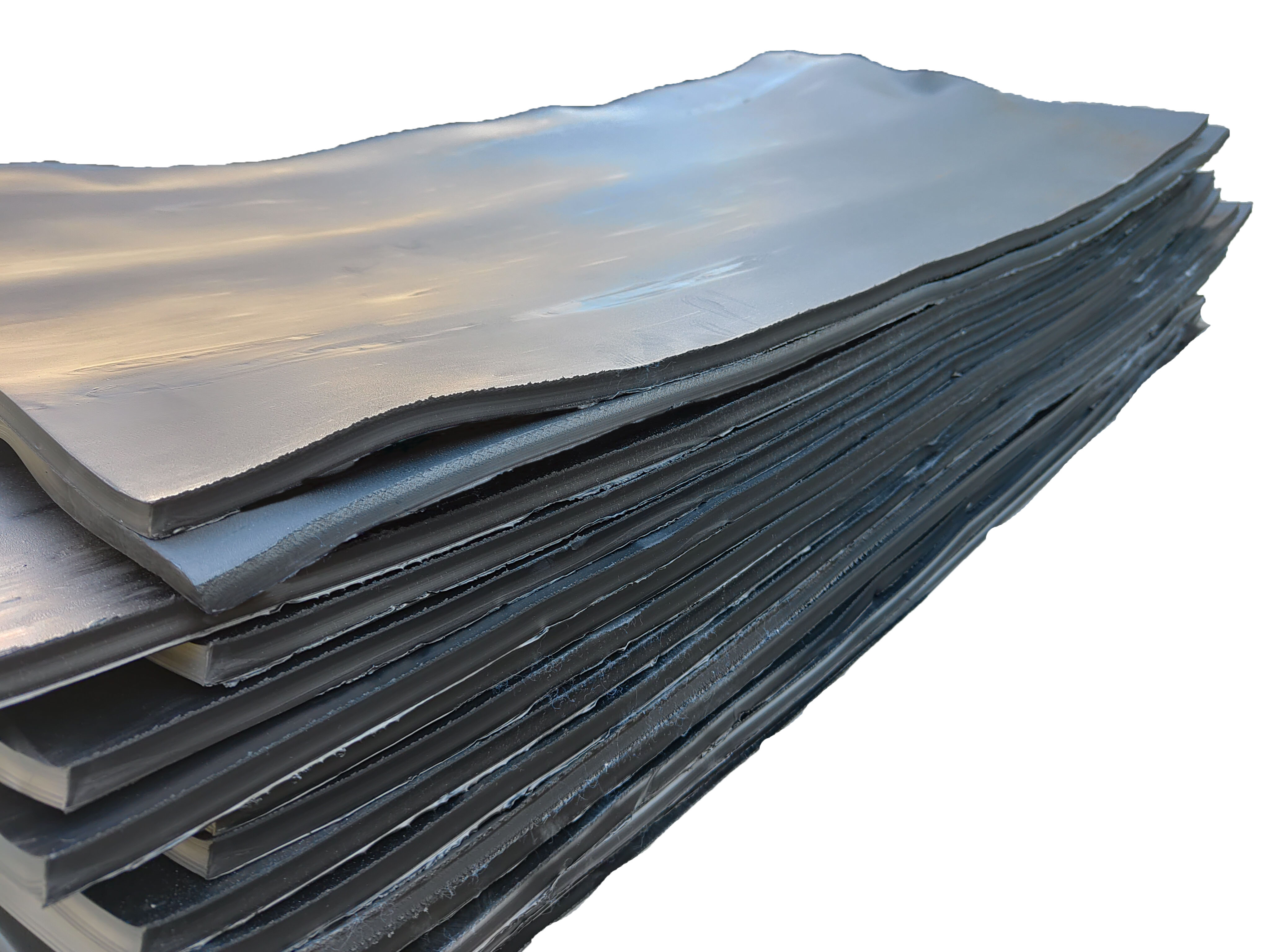
rubber conveyor belt material
Mainly used as a reinforcing agent and filler in rubber, its consumption accounts for about half of the total rubber consumption. Carbon black used in rubber makes up 94% of the total carbon black production. Additionally, it serves as a coloring agent in inks, paints, and plastics, as well as a UV light shield for plastic products. In many other applications, such as electrodes, dry cells, resistors, explosives, cosmetics, and polishing pastes, it is also an important additive.
Carbon black is primarily used in rubber products. The finer the particle size of carbon black, the better its reinforcing properties; the higher the degree of structure, the greater its tensile strength and modulus. Fine-grained reinforcing varieties are mainly used for tire treads, providing excellent wear resistance. Other parts of the tire, such as the sidewalls, carcass layers, belt cushion layers, and inner liner layers, require the compound to be resistant to flex cracking, ozone oxidation, have good resilience, and low heat generation. Generally, coarser semi-reinforcing (specific surface area below 40 m²/g) furnace black is selected.
Black pigment is widely used in ink, coatings, and plastics. Ink, especially newsprint ink, primarily uses medium black pigment. In the manufacturing of coatings, high-black pigment gives advanced automotive topcoats their blackness and gloss, while medium black pigment is used for general industrial coatings. Additionally, medium black pigment is commonly used as a UV shield for polyolefins to enhance the weather resistance of plastic products. Black pigment for rubber is mainly used in tire compounds, particularly for off-road and engineering tires, providing high strength and excellent wear resistance.
Thermal cracking black is mainly used for rubber products. Because of the coarse particle size and poor reinforcement performance, it is only used in occasions requiring maximum filling increment, such as manufacturing rubber pads, rubber tubes, sponge products, sealing rings, tire lining layer, bead glue and insulation products.
High pigment series carbon black (HCC) | Pigment series carbon black (MCC) | Common pigment carbon black (RCC) | |
function | Carbon black by post-treatment gas | Carbon black by post-treatment gas | Carbon black by post-treatment furnace |
Specific surface area (BET) | 280-350m2 /g | 150-200m2/g | 120-145m2 /g |
PH price | 2.0-3.5 | 3.5-5.0 | 6–8 |
volatile matter | 5%-8% | 3%-5% | 0.5%-1.0% |
fineness | 10-15 μ m | 10-15 μ m | 10-15 μ m |
apply | Fine grain, easy to disperse, slightly acidic, good wetting. Large specific surface area, high blackness, good gloss, high coloring, blue phase, widely used in automobile paint, high grade paint, offset ink, ink paste, toner and engineering plastics. | Fine particle size, good wetting and solubility, lower specific surface area than the special black series, easier to disperse, medium and high blackness and coloring force, blue phase. It can be widely used in various paints, inks and architectural coatings, color masterbatch | Low structure, can have low viscosity, high flow, easy to process and disperse, blue phase. Good performance and other characteristics are suitable for: water-based news inks: such as flexographic printing inks, thermosetting roll printing inks, ordinary paint color mother and ordinary paint, color mother. |
Meaning of technical indicators | |
specific area | The BET (Brunauer-Enmet-Teller) low temperature nitrogen adsorption method can be used. The simple iodine adsorption method, which is commonly used in the world, can also be used. The measurement results represent the surface area per gram (m2/g). |
grain size | The particle size of each type of carbon black listed in the table is the original particle size of carbon black, which is measured by electron microscope and is the average value of a certain number of particles. |
coloring power | It represents the ability of carbon black to dye white body, generally with high coloring power and good covering performance. The test method is carried out according to ASTM-3265. |
Absorption value (DBP absorption value) | The adsorption of carbon black is carried out by using phthalic acid = methyl ester = butyl ester (DBP). The amount of DBP consumed when the adsorption equilibrium is reached represents the size of carbon black structure. The higher the adsorption value, the higher the carbon black structure; otherwise, it is lower. |
volatile matter | The content of oxygen-containing functional groups (carboxyl group, quinone group, lactone group and hydroxyl group) adsorbed on the surface of carbon black represents the surface chemical properties of carbon black. It is related to PH value. |
PH price | It represents the acidity and alkalinity of carbon black. Generally, furnace carbon black is alkaline (PH> 7). Only after post-treatment, the PH value of carbon black is between 3 and 5 and the volatile content is high. |
Manifest density | The weight of carbon black per unit volume, namely (g/l), is the size of the space occupied by various types of carbon black. The larger the granulation, the greater the apparent density, and vice versa. Granulation has an effect on the dispersibility of carbon black (especially used in plastics and paints\inks). |
heating loss | The moisture content of carbon black is measured at a certain temperature, which is related to the generation environment of carbon black. |
carbon black | High-pigment carbon black, medium-pigment carbon black, ordinary pigment carbon black, water-soluble carbon black, eco-friendly carbon black, insulating carbon black, high-temperature resistant carbon black, ink-grade carbon black, paint-grade carbon black, sealant-grade carbon black, color masterbatch-grade carbon black, synthetic fiber-grade carbon black, color paste-grade carbon black, leather-grade carbon black, cement-grade carbon black, ceramic-grade carbon black, cyanotype pigment carbon black, plastic ink-grade carbon black, PVC cable material-grade carbon black, film-forming color masterbatch-grade carbon black, silicone-copper adhesive-grade carbon black, paper coloring-grade carbon black, epoxy floor coating-grade carbon black, automotive paint-grade carbon black, anti-corrosion paint-grade carbon black, and various other mid-to-high-end pigment carbon blacks! |
. reinforcing action
Carbon black significantly improves the physical and mechanical properties of vulcanized rubber by increasing the interaction force between rubber molecules, including:
Tensile strength and tear resistance: fine particle size carbon black (such as super wear resistant carbon black N110) can form a more compact network structure, enhance the bearing capacity of rubber.
Wear resistance: carbon black with high specific surface area (such as high wear resistant carbon black N330) can reduce the coefficient of friction and prolong the service life of tires and other products.
Fatigue resistance: Carbon black dispersed in rubber can delay crack propagation and improve dynamic performance.
- Filling and cost control
As a filler, carbon black can replace part of the raw rubber (the amount is usually 20%~70%), reducing the production cost.
Carbon black of different particle sizes (such as soft carbon black and hard carbon black) can balance performance and cost according to demand.
- Function optimization
Weather resistance: carbon black absorbs ultraviolet light and delays rubber aging.
Conductivity: specific carbon black (such as conductive slot carbon black CC) is used for anti-static or conductive rubber products.
Processing performance: Alkaline carbon black (such as furnace carbon black) can promote vulcanization and shorten the production cycle.
- Other auxiliary functions
Improve the blackness and appearance uniformity of rubber.
Improve oil resistance and chemical corrosion resistance, suitable for special environment.
Conclusion: Carbon black is an indispensable reinforcing material in the rubber industry. Its role covers the improvement of mechanical properties, cost optimization and multifunctional modification. The specific effect depends on the type of carbon black (such as particle size, structure, surface chemical properties) and the proportion of addition.
Leave a Reply
Want to join the discussion?Feel free to contribute!