Vulcanized rubber
Sulcanized rubber refers to the vulcanized rubber, has the same sticky, not easy to break and other characteristics, rubber products are mostly made of this rubber. Also called ripe rubber, commonly known as rubber or rubber skin. General term of rubber material after vulcanization processing. After vulcanization, the raw gelatin forms a spatial stereo structure, which has high elasticity, heat resistance, tensile strength and insolubility in organic solvents. Most of the rubber products are vulcanized rubber.
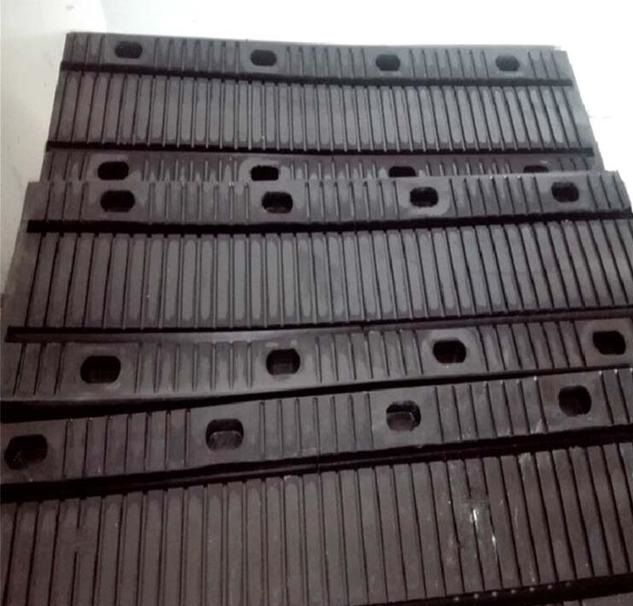
vulcanizing rubber
Sulphur rubber system
unsaturated rubber
The following several types of vulcanization systems are usually used.
(1) They mainly include sulfur, organic disulfides and polysulfides, thiazoles, diphenylguanidines, zinc oxide and stearic acid. This is the most versatile vulcanization system. However, the thermal and oxygen-resistant aging performance of the produced sulfide rubber is not high.
(2) Alkyl-phenolic aldehyde resin.
(3) Polyhalides (such as hexachloroethane for polybutadiene rubber, styrene butadiene rubber and nitrile rubber) and hexachlorop-xylene.
(4) Dual functional reagents [such as quinones, diamines, azoles and phenyl azo derivatives (for butyl rubber and ethyl propylene rubber), etc.
(5) Double maleimide, diacrylate. Acrylate (methacrylate), prepolytheracrylate.
(6) Organic peroxides used for vulcanized saturated rubber.
saturated rubber
(1) When thializing EPDM, organic peroxides and unsaturated crosslinking reagents are used, such as triallyl isocyanurate ester (TAIC).
(2) Organic peroxides can also be used in silicone sulfide rubber. It can be done under the condition of catalyst (Pt).
Rubber vulcanization process
According to the vulcanization conditions, it can be divided into cold, room temperature and hot sulfide.
cold cure
Cold sulfide can be used for the sulfide of thin film products, which are impregnated in a carbon disulfide solution containing 2%~5% sulfur chloride, and then washed and dried.
room temperature cure
At room temperature sulfation, the sulfuration process is carried out at room temperature and atmospheric pressure, such as using room temperature vulcanation gel (mixing solution) for bicycle tire joint, repair, etc.
heat cure
Thermal vulcanation is the main method of vulcanation of rubber products. According to the different sulfide media and sulfide modes, thermal vulcanation can be divided into three methods: direct, indirect and mixed gas vulcanation.
(1) Direct vulcanization, products directly into hot water or steam medium vulcanization.
(2) Indirect vulcanization, products placed in the hot air in the sulfide, this method is generally used for some products with strict appearance requirements, such as rubber shoes.
(3) Mixed vulcanization, first use air vulcanization, and then use direct steam vulcanization. This method can not only overcome the disadvantage of steam vulcanation affecting the appearance of products, but also overcome the disadvantage of slow heat transfer by hot air, long vulcanation time and easy aging.
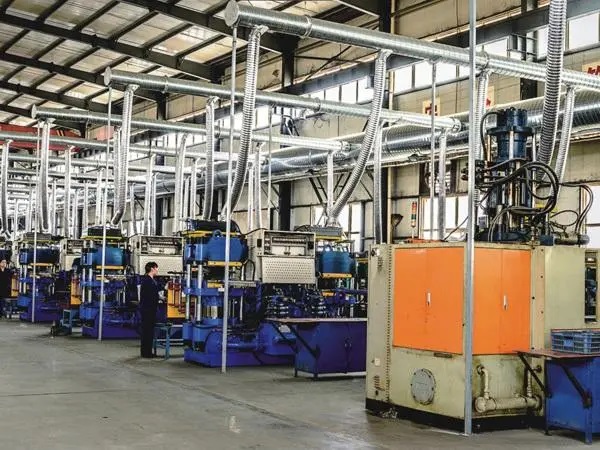
vulcanizing machine
influencing factor
Major factors affecting the vulcanization process
(1) Amount of sulfur used. The larger the dosage, the faster the vulcanization, the higher the degree can be achieved. The solubility of sulfur in rubber is limited, and excessive sulfur will precipitate from the surface of the rubber material, commonly known as “sulfur spray”. To reduce the sulfur spraying phenomenon, it is required to add sulfur at the temperature as low as possible, or at least below the melting point of the sulfur. According to the use requirements of rubber products, the amount of sulfur in soft rubber is generally not more than 3%, the amount of semi-hard rubber is generally about 20%, the amount of hard rubber can be as high as 40%.
(2) Sulfide chemical temperature. If the temperature is 10℃ high, the vulcanization time is shortened by about half. Because rubber is a bad thermal conductivity, the difference of the temperature. In order to ensure a relatively uniform degree of vulcanization, thick rubber products generally use gradual warming, low temperature for a long time vulcanization.
(3) Sulcanization time. This is an important part of the vulcanization process. Time is too short, the degree of vulcanization is insufficient (also known as undersulfur). Time is too long, the degree of sulfation is too high (commonly known as oversulfur). Only the appropriate degree of vulcanization (commonly known as positive sulfide), to ensure the optimal comprehensive performance.
The deformation factor
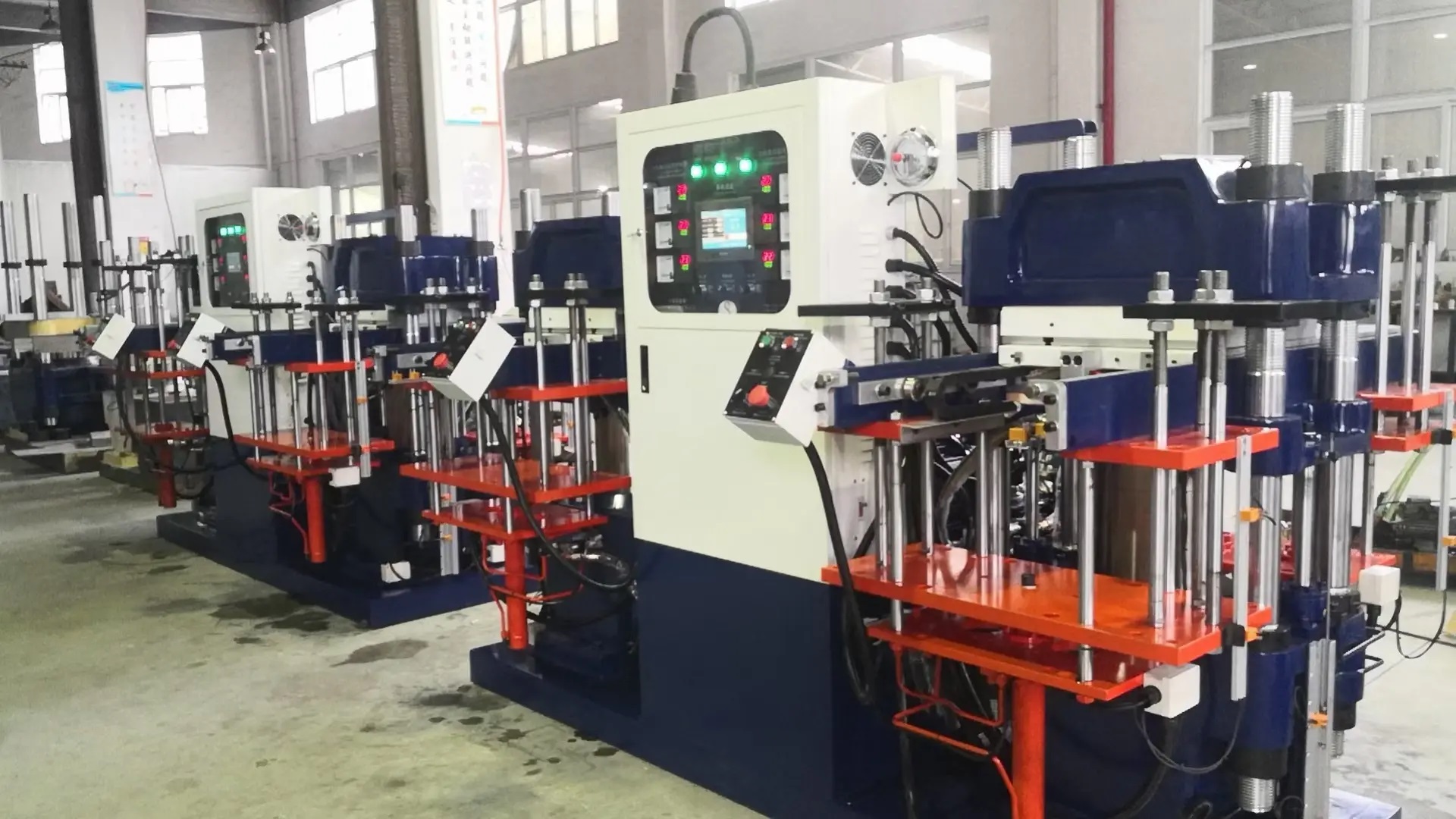
vulcanizing work shop
Compressed permanent deformation is one of the important performance indexes of rubber products. The size of the compressed permanent deformation of the sulfide rubber involves the elasticity and recovery of the sulfide rubber. The size of the permanent deformation is mainly dominated by the changes in the recovery ability of the rubber. The factors affecting the recovery ability include the force (viscosity) between molecules, the change or destruction of the network structure, the displacement between molecules, etc. When the deformation of the rubber is caused by the stretching of the molecular chain, its recovery (or the size of the permanent deformation) is mainly determined by the elasticity of the rubber: if the deformation of the rubber is accompanied by the destruction of the network and the relative flow of the molecular chain, this part can be said to be irreversible, it has nothing to do with the elasticity. Therefore, all the factors affecting the elasticity and recovery of rubber affect the permanent deformation of vulcanized rubber. These factors include elasticity, strike elasticity (resilience), elasticity and modulus, compression permanent deformation, tearing permanent deformation, etc.
1, elasticity —— The elasticity of rubber should be a theoretical concept, it represents the difficulty of rotation in the rubber molecular chain segment and side base, or the flexibility of the rubber molecular chain and the intermolecular force. For the vulcanized rubber, its elasticity is also related to the density and regularity of the crosslinking network.
2, elasticity and broken permanent deformation —— often said that the elasticity of natural rubber is very good, but its broken permanent deformation is often very large, this is mainly the natural rubber elongation is very large, the elongation process caused by the damage of the network and the displacement of the molecular chain is very large, the recovery process after fracture is long and the unrecoverable part of the increase. If the permanent deformation of zhong length is compared, the permanent deformation of natural rubber is not necessarily very large.
3, strike elasticity or resilience is determined under the condition of fixed load (or fixed energy), the size of its elasticity has a direct relationship with the crosslinking degree [1] or modulus of vulcanized glue, expressing the synthesis of rubber elasticity and viscosity (or absorption).
4, compression permanent deformation is measured under fixed deformation conditions, the size of its value is related to the elasticity and resilience of rubber.
In the range of higher strain rate, the dynamic stress-strain relationship of vulcanized rubber is related to the strain rate, and the elastic modulus, yield stress and flow stress all increase with the strain rate, so the material shows obvious strain rate effect in the dynamic experiment. But under low strain rate loading.
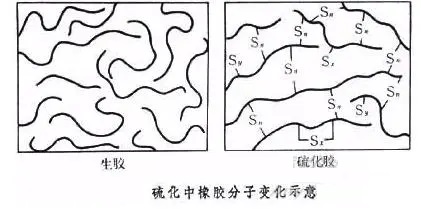
rubber cell constructure
Fragile test
The highest temperature when the sample is damaged under the specified conditions is the brittle temperature, which can compare the performance of non-hard plastics and other elastic materials at low temperature conditions. The brittle temperature and low temperature performance of different rubber materials or different formulations can be determined. Therefore, no matter in the scientific research materials and their products quality inspection, production process control and other aspects are indispensable.
thermoplasticity
brief introduction
Thermoplastic vulcanized rubber, referred to as TPV, but the name is easy to be confused with other kinds of thermoplastic elastomers, because usually thermoplastic elastomers is also called thermoplastic rubber, especially styrene elastomers, currently at least in China seems to “TPR” has become its proprietary name, a mention TPR, is to SBS, SEBS styrene based as thermoplastic elastomers, this and styrene elastomers in civil and large consumption of terminal consumer goods is inseparable.
Hyperplastic thermoplastic rubber name if say a little detail, it should be thermoplastic dynamic sulfized rubber, added “dynamic” 2 word is more specify the production of the thermoplastic sulfide rubber process —— dynamic sulfurization, this process refers to the rubber and thermoplastic melting mixing process make the rubber sulfization, of course in the rubber in the sulfur also constantly mixed with thermoplastic phase, so the sulfide rubber is distributed in thermoplastic continuous phase. The corresponding thermoplastic static vulcanized rubber means that the rubber is vulcanized by the traditional method, and then ground the vulcanized rubber into powder through the grinding equipment, and finally mixed with the molten thermoplastic. Theoretically, this method can also produce TPV with excellent performance, but so far, it is only in the laboratory stage.
Composition of the thermoplastic vulcanized rubber
The TPV is mainly composed of two parts, one is plastic, as a continuous phase, and the other is rubber as a dispersed phase. Usually the rubber needs to cooperate with the softening oil or the plasticizer. Sulfide agents and some auxiliary aids are also essential. In addition, in order to reduce costs or improve certain performance, some inorganic fillers will be filled.
TPV can be formed between many plastics and rubber, but only individual blends have practical value after dynamic sulfation, and the current commercial ones are PP / PE / EPPM, PP / NBR, PP / ACM, and PS / SEBS. In the book Thermoplastic elastomer, 10 comments on 99 kinds of rubber / plastic blend prepared from 11 kinds of rubber and 9 kinds of plastics, it is found that to obtain the best performance of the dynamic vulcanized blend of rubber / thermoplastic plastics, the following conditions must be met:
(1) The surface energy of plastic and rubber two polymers can match;
(2) Low length of rubber tangle molecular chain;
(3) The crystallinity of plastic is greater than 15%. When the polarity or surface energy difference between plastic and rubber is relatively large, add the appropriate compatible agent, and then dynamic sulfation, can also get excellent performance blend.
Regeneration research
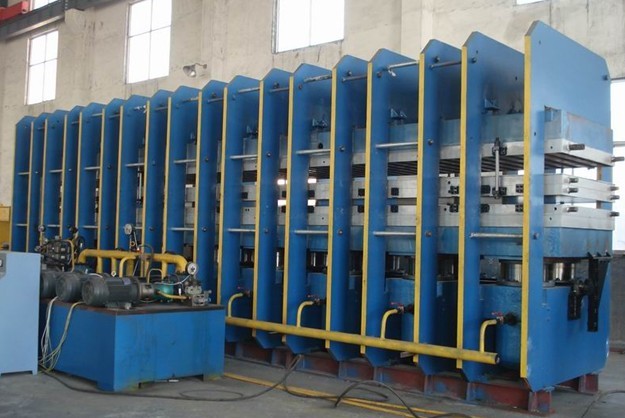
plate vulcanizing machine
Rubber products in the process of production and use of a large number of waste vulcanized rubber, has become the main challenge in the development of rubber industry. Waste rubber is a thermosetting polymer material, which is insoluble under conventional conditions and difficult to degrade under natural conditions. Its recycling and regeneration technology has always been a worldwide problem, which is related to the global environmental protection and sustainable utilization of resources, so it has attracted more and more attention in the industry. Reced rubber is recycled in waste rubber, which plays an important role in the rubber formula system as a filler. Although the addition of recycled glue will reduce the physical and mechanical properties of raw glue, such as tensile strength, modulus, tear strength, etc., but it can provide the characteristics that raw glue does not have. On the one hand, it can shorten the mixing time, reduce the energy consumption of the adhesive in the mixing process; secondly, in the process of extrusion or rolling is faster, when the mixing glue contains recycled glue, extrusion expansion and rolling shrinkage can be avoided; third, when the recycled glue can play an anti-aging effect, its effect is better than the remaining anti-aging agent. It is of great significance to understand the reaction mechanism of generating regenerative glue and the preparation process of recycled glue for better research of recycled glue.
Leave a Reply
Want to join the discussion?Feel free to contribute!